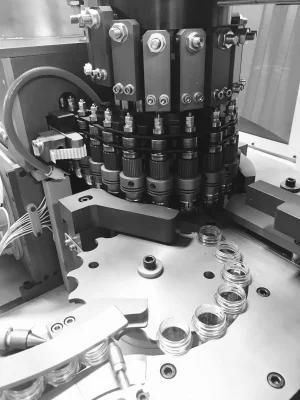
Plastic Bottle Blowing Molding Machine Bottle Making Machine
Jiangsu Faygo Union Machinery Co., Ltd.- Type:Stretch Blow Molding Machine
- Cavity Number:4
- Hourly Outpu:7200bottles,Hour(@500ml)
- Working Power:20kw
- High Pressure Require:6m3,30bar
- Motors:Servo Motor Control
Base Info
- Model NO.:FG4
- Blowing Valve:American Parker
- Electrical Element:Mistubishi,Siemens
- Raw Material:PET
- Making Method of Parison:Stretch Blow
- Automation:Automatic
- Computerized:Computerized
- Certification:CE, ISO9001:2008
- Transport Package:Wooden
- Specification:ce
- Trademark:Faygo
- Origin:China
- HS Code:8402119000
- Production Capacity:100PC Yearly
Description
Basic Info.
Model NO. FG4 Blowing Valve American Parker Electrical Element Mistubishi/Siemens Raw Material PET Making Method of Parison Stretch Blow Automation Automatic Computerized Computerized Certification CE, ISO9001:2008 Transport Package Wooden Specification ce Trademark Faygo Origin China HS Code 8402119000 Production Capacity 100PC YearlyProduct Description
Specifications
Model | 4 cav |
Capacity | 7200B/H |
Bottle type | 250-2000ml |
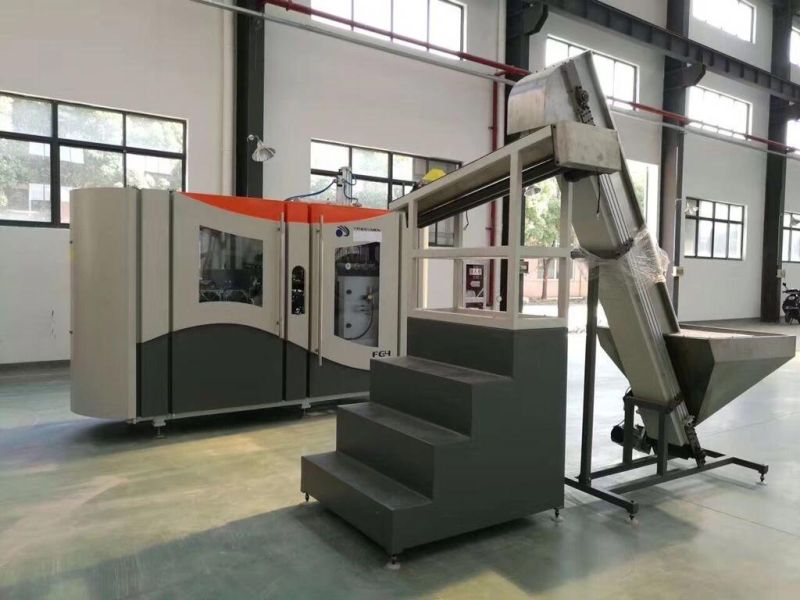
Automatic PET Bottle Blowing Machine
I. Brief Introduction:
FG4 is the new generation of linear blowing machine. Comnpared with traditional blowing machine, It has 3 improvement:
1)High speed: China first blowing machine whose single mold speed can reach 1800 BPH. FG4 has 4 cavities, production speed is 6800-7200BPH.
2) Energy saving: It has only 2 lamp boxes, at least 20000USD can be saved per year, electrical ammeter is equipped, you can know how much every single bottle costs you.
3) High Reliability: Machine adopts modularized design principle, the movement is integrated in 3 sets servo motor, which promises this machine will have good condition under full load operation.
II. Technical Features:
1. Servo driving and cam linking movement blowing section:
The unique cam linking system integrates mold-opening, mold-locking and bottom mold-evevating in one movement, equipped with high speed servo motor, which greatly shortens the blowing cycle and accelerates the spped.
2. Minimize distance of heating heads,maximize the heating efficiency.
Heater distance in the heating oven is minimized to 38.1mm, compared with the conventional heating oven it can save more than 30% consumption.Equipped with the air cycling system and redundant heating discharge system it ensures constant temperature in the heating zone.
3. Efficient and soft perform inlet system,ensure the spped and preform protction.
By rotary and soft preform loading system, the speed of preform feeding is ensured, meanwhile, the preform neck is well protected.
4. Modularized design conception, convenient for maintenance and changing changeovers
The machine adopts modularized design concept to make it convenient and cost-saving for the maintenance and changing changeovers.
One Stop Station Services
1) Stand-by engineers team to provide overseas installation and commissioning service.
2) 1 year warranty. During warranty, we provide free of charge for repairing cost.
3) Lifetime maintenance. After-sales department can provide life long maintenance service.