
Sjsp138/32 Parallel Twin Screw Spc Production Line
Wuxi Boyu Plastic Machinery Co., Ltd.- Type:Sheet Extruder
- Plastic Processed:PVC
- Product Type:Extrusion Molding Machine
- Feeding Mode:One Feed
- Assembly Structure:Integral Type Extruder
- Screw:Twin-Screw
Base Info
- Model NO.:SJSP138,32
- Engagement System:Conical Meshing
- Screw Channel Structure:Deep Screw
- Exhaust:Exhaust
- Automation:Automatic
- Computerized:Computerized
- Screw Design:Conical Twin-Screw
- Weight:~44.5 Tons
- Power:485-750kw Per Line
- Voltage:220-415V , 50-60Hz 3 Phase
- Function:Flooring Sheet Extrusion
- Certificate:Ce, ISO, TUV, UL, CSA
- Transport Package:Wooden Case Packing or Film
- Specification:Production Line layout: 50m (L) * 5m (W) * 8m (H)
- Trademark:Boyu
- Origin:Wuxi China
- HS Code:8477209000
- Production Capacity:200 Lines Per Year
Description
SJSZ 138/32 parallel twin screw extrusion lineNO. Machine Item Qty Unit 2.01 138/32 parallel twin screw extruder 1 Set 2.02 Five-Rollers Calendar 1 Set 2.03 On-line EIR Hardware 1 Unit 2.04 Rollers oil Heating System 1 Unit 2.05 Wind Curtain Machines 6 Set 2.06 Traction Machine 1 Set 2.07 Air cooling cabinet 1 Set 2.10 Stainless steel roller conveyor 1 Unit 2.11 Slabs cutting machine 1 Unit 2.12 Automatic flipping & Stacking System 1 Unit 2.13 Automatic transposition stacking pallet 1 Unit 2.14 1350mm extrusion T-die 1 Pc
III.Production Flow
Material mixing → Extruder → Calender→ Cut-to-length →Stacking →UV coating →Saw cutting →
Slick slotting →Backing limitation →QC inspection → Packing
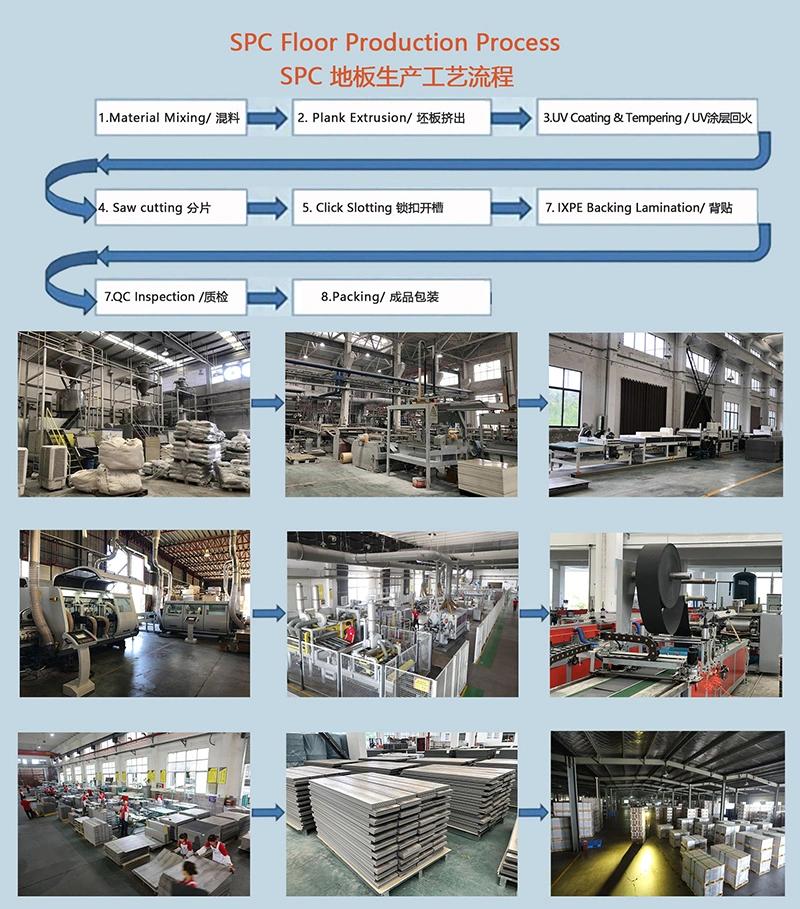
IV. Main Processing Steps
1. Material Mixing→ screw conveyor from 8m3 Silo (~5 Tons) → Feeding recipe material into the hopper loader → Extruder → Material Plasticizing → Extrusion through T-die → Five Roller Calender
2. Plank extruded from T-die→ Five Roller Calender →Thickness calibration on 1# & 2 # rollers → Wearing film & decorative film laminating on 3 # roller → Temperature reduction on 4# silicon roller → On-line embossing (EIR) on 5# roller → Edges trimming
3. Plate conveying from 5 roller calender→ Edges Trimming → Roller Cooling Bracket →Air Cooling Cabinet → Traction Machine→ Cut-to-length machine →Automatic Flipping & Stacking Machine
V. Advantages of BOYU WPC Production Machine Line
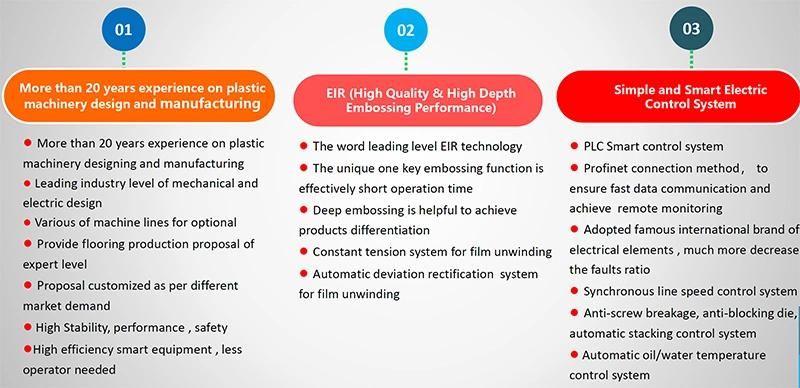
VI.Services
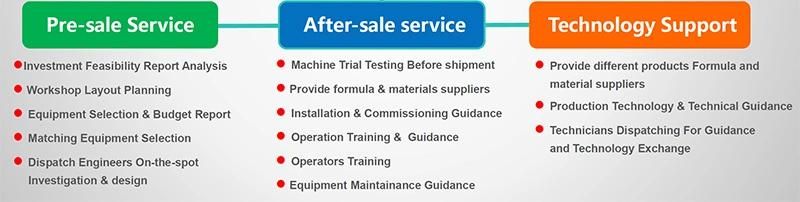
VII. Project Case
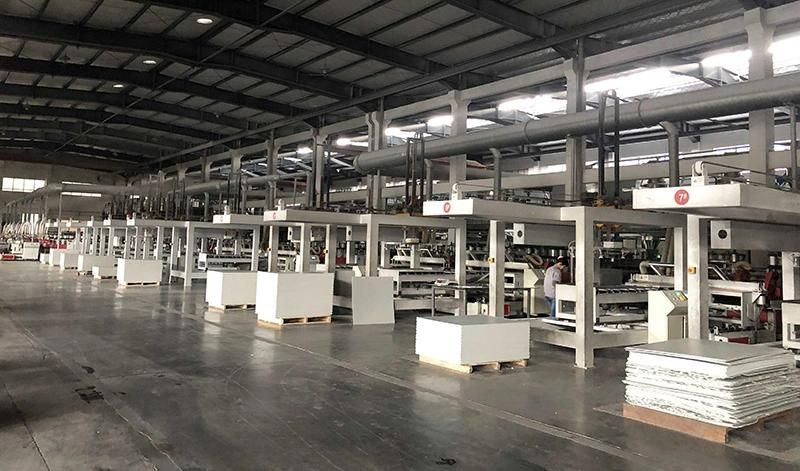
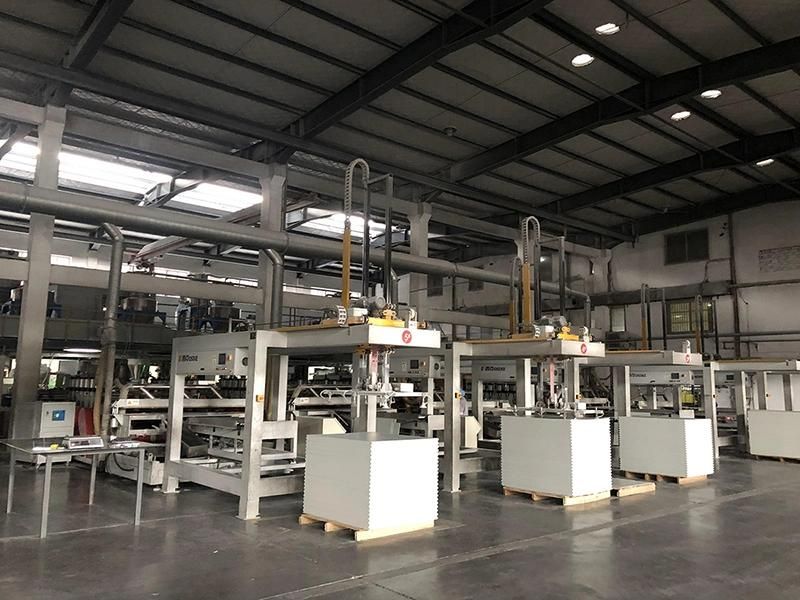

VII. Boyu Company Profile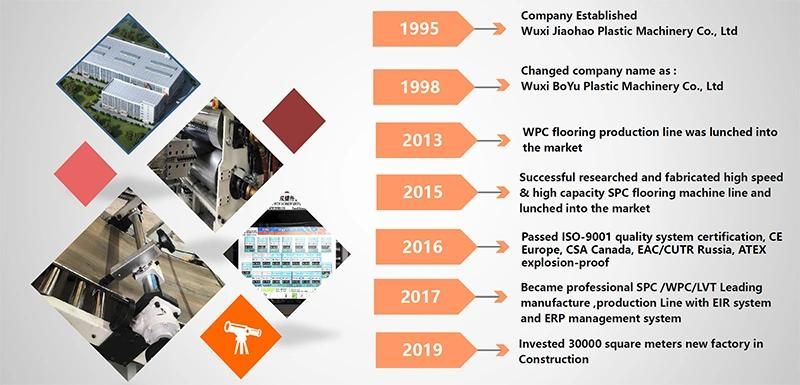
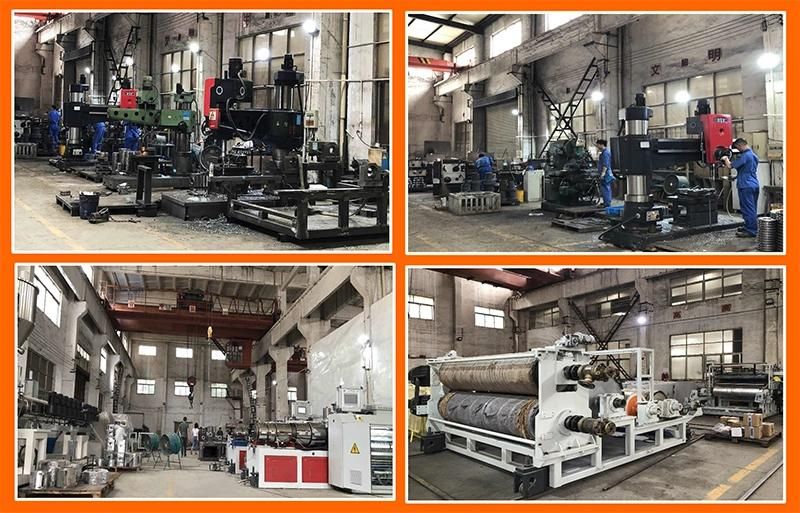
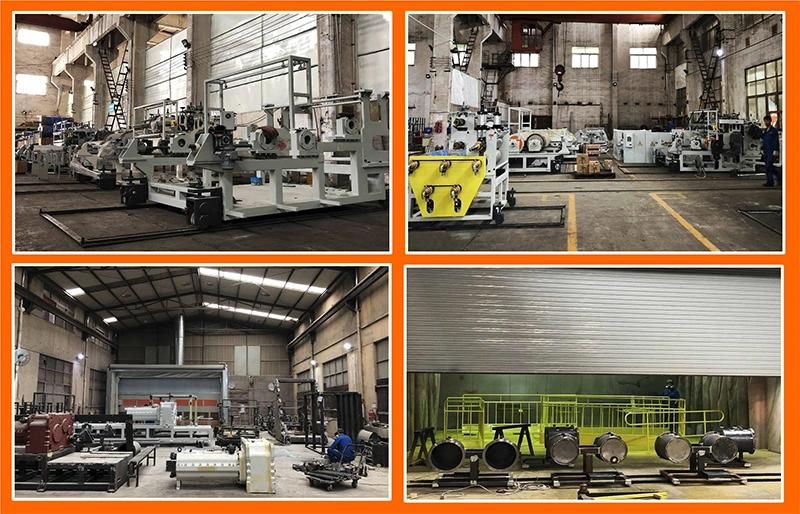
VIII. Patents Certificates
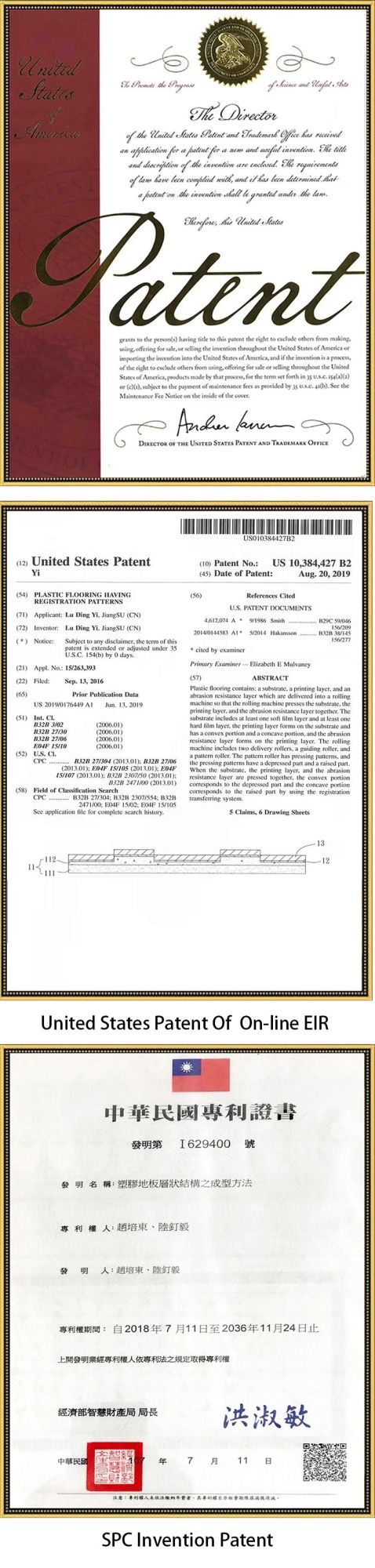
III.Production Flow
Material mixing → Extruder → Calender→ Cut-to-length →Stacking →UV coating →Saw cutting →
Slick slotting →Backing limitation →QC inspection → Packing
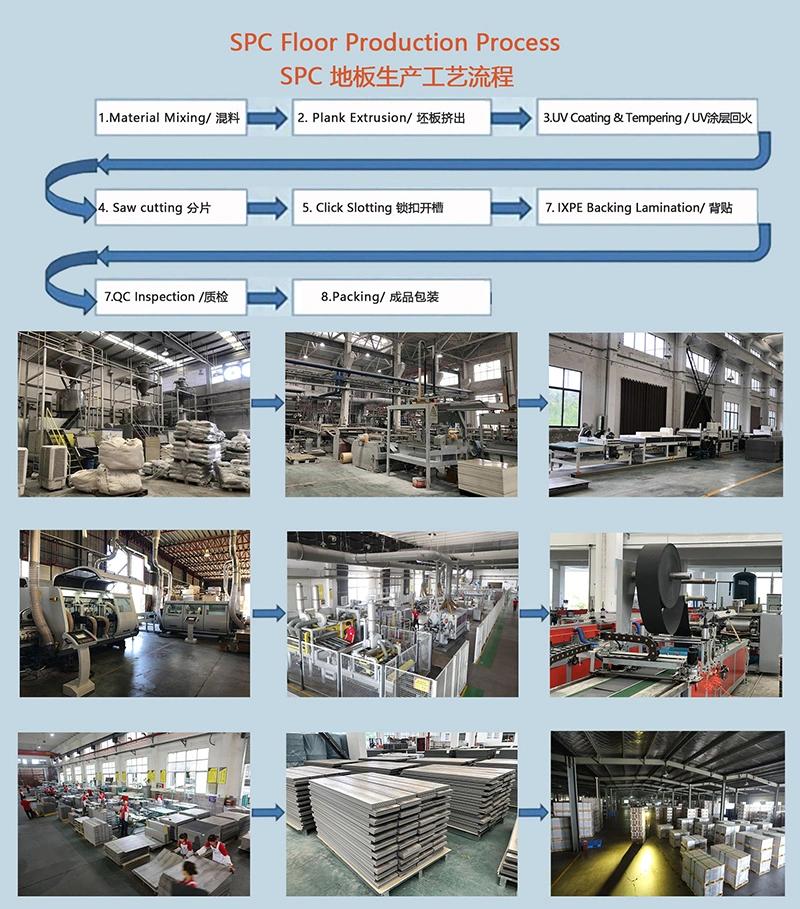
IV. Main Processing Steps
1. Material Mixing→ screw conveyor from 8m3 Silo (~5 Tons) → Feeding recipe material into the hopper loader → Extruder → Material Plasticizing → Extrusion through T-die → Five Roller Calender
2. Plank extruded from T-die→ Five Roller Calender →Thickness calibration on 1# & 2 # rollers → Wearing film & decorative film laminating on 3 # roller → Temperature reduction on 4# silicon roller → On-line embossing (EIR) on 5# roller → Edges trimming
3. Plate conveying from 5 roller calender→ Edges Trimming → Roller Cooling Bracket →Air Cooling Cabinet → Traction Machine→ Cut-to-length machine →Automatic Flipping & Stacking Machine
V. Advantages of BOYU WPC Production Machine Line
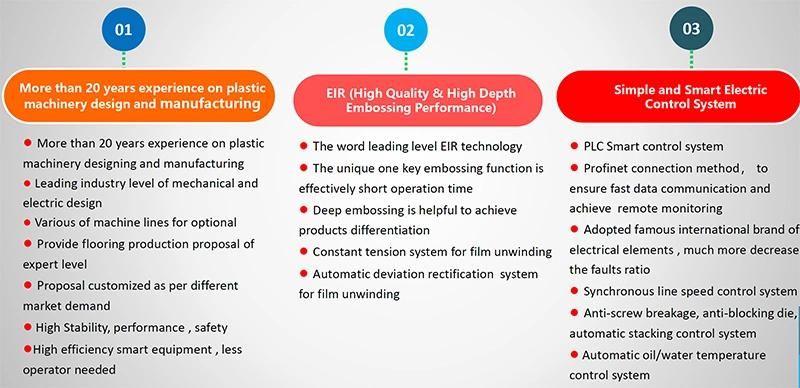
VI.Services
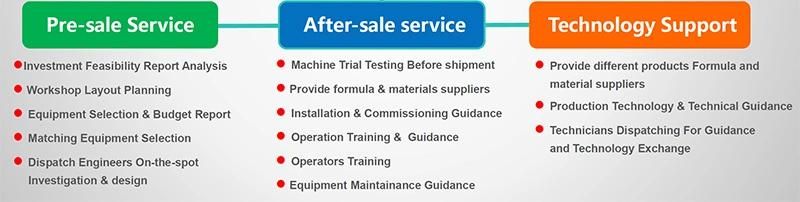
VII. Project Case
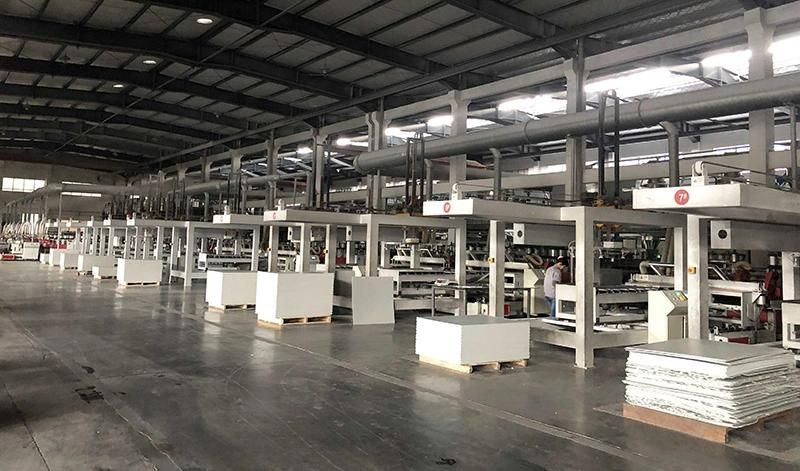
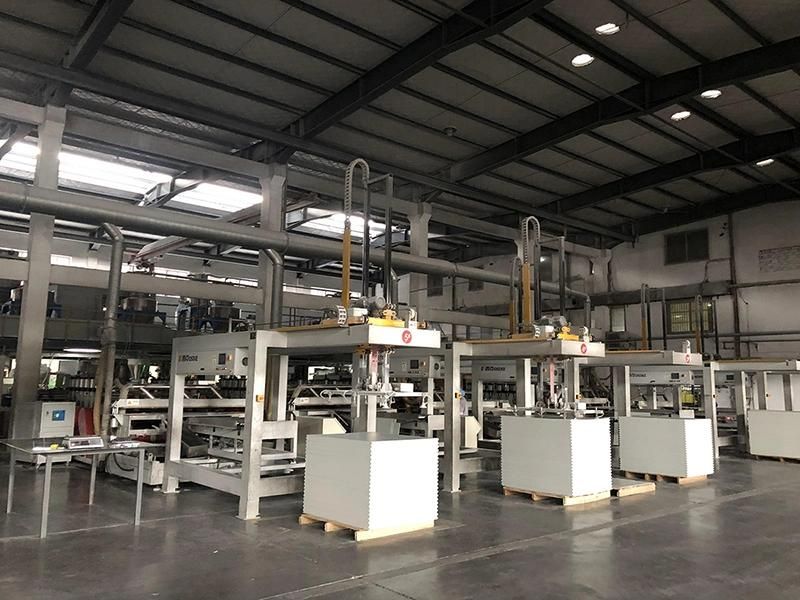

VII. Boyu Company Profile
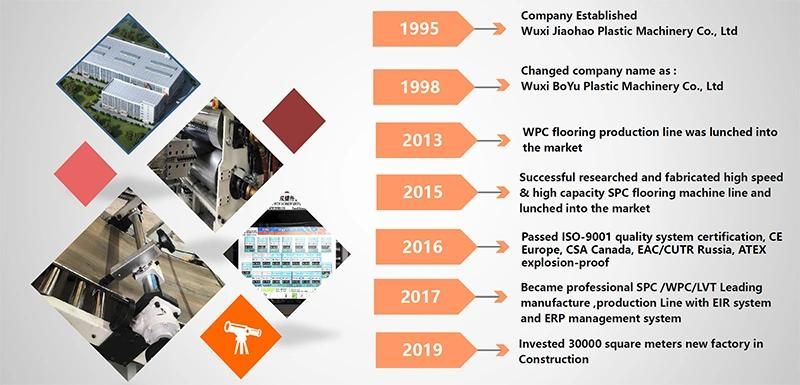
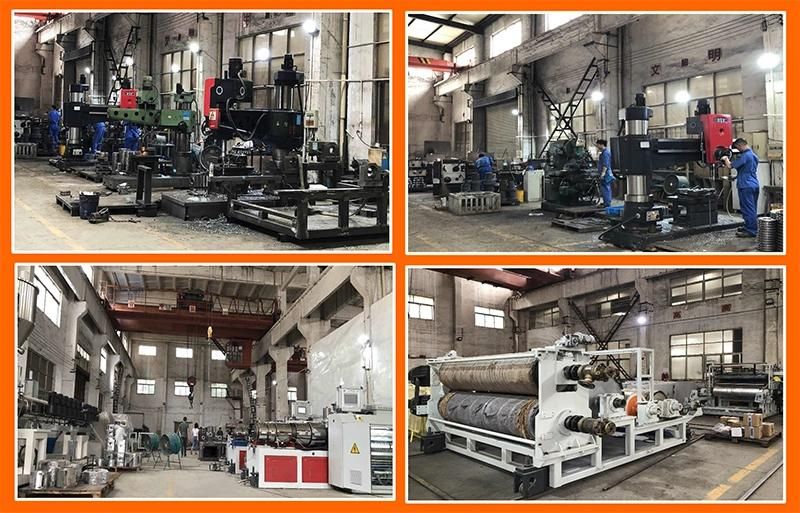
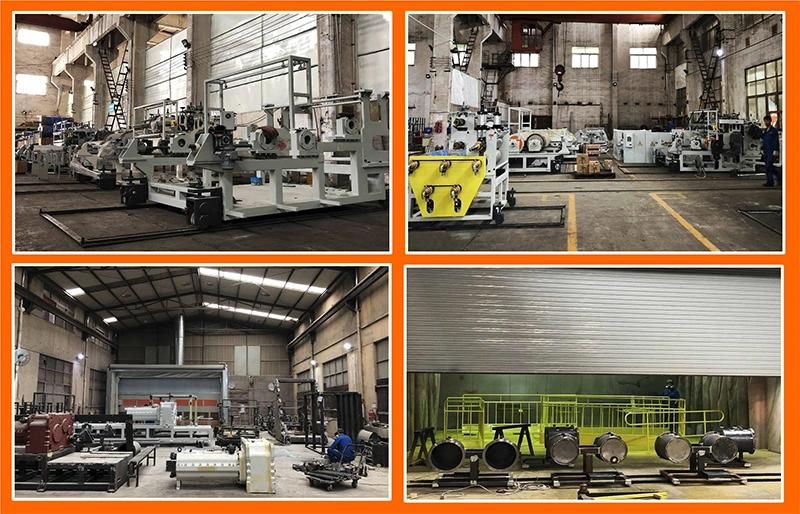
VIII. Patents Certificates
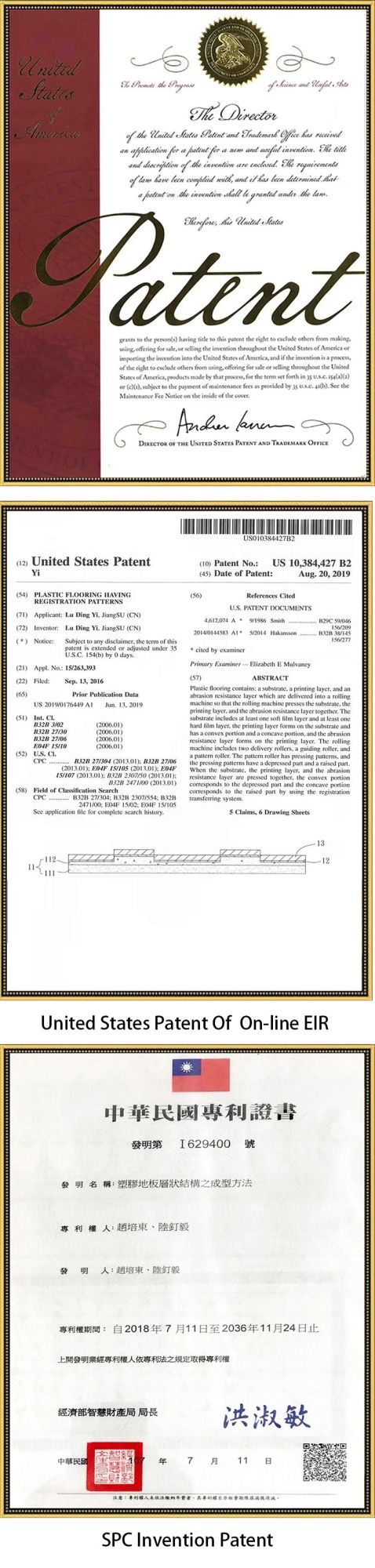